USA-Made Racer Elite Connecting Rods Deliver Factory-Level Performance
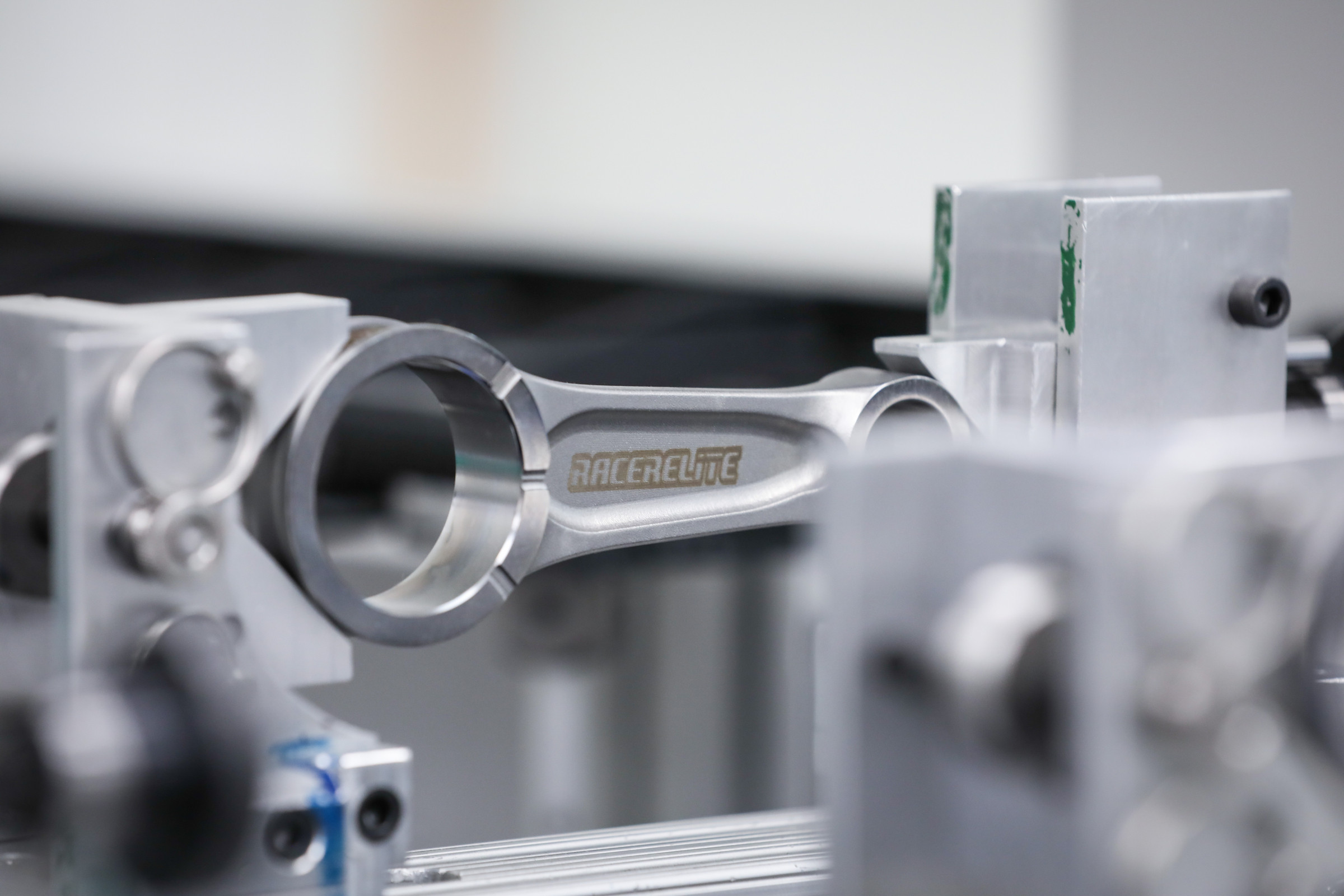
A rider may not give much thought to their motorcycle’s connecting rod—until one of two things happen: the rider is interested in improving the performance of their engine or is the unfortunate victim of a broken or “thrown” rod. Regardless of situation, it’s important to understand that a connecting rod is the crucial link between the piston and crankshaft.
A connecting rod is constantly under a tremendous load. Increasing horsepower—whether through a high-compression piston, camshafts, exhaust pipe, or other hop-ups—magnifies that stress and load. The good news is that Wiseco’s Racer Elite rod is designed to handle higher engine loads, more horsepower, torque and/or a higher RPM range, all while maintaining improved wear characteristics.
Manufacturing & Materials
Proudly made in the USA from start to finish, every Wiseco Racer Elite connecting rod is made from proprietary, USA-made steel forgings for better-aligned grain flow. Different heat-treating methods are used in order to control hardness in the beam versus on the thrust faces. This results in a stronger product with extended service life. Engineers focused on removing weight from the big end of the rod while ensuring a wider thrust face for better heat transfer. Precision CNC machining holds tolerances up to thousandths of an inch and allows for strength-to-weight optimization throughout the connecting rod.
“We roll in a bronze bushing with a proprietary method that really captures the bushing in the rod itself,” explains Scott Highland, Director of Powersports for Wiseco. “There are very tight tolerances in design and machining, holding less than two-thousandths of an inch on the center-to-center, but maintaining other critical dimensions such as big- and small-end width to less than ten thousandths of an inch.”
Oil lubrication slots are machined on the big end of the rod. Chamfered edges and relieved oil slots increase long-term durability. The small end of the Wiseco connecting rod features a proprietary oiling method on the top, which helps retain more strength in the inertia forces that are generated on the rod.
Initial applications of the Racer Elite rods will utilize needle bearing and cage style big end bearings, a traditional and proven technology in powersports engines. However, several late model dirt bike applications are now equipped with plain bearing style big end bearings, a technology common in the automotive world. Racer Elite will soon be offered in plain bearing configurations as well for certain applications for a highly advanced connecting rod package.
Once clearing the machining phase, each rod undergoes a dedicated quality inspection process. Zeiss CMM equipment measures key dimensions, such as center-to-center distance, big-end width, small-end width, and small-end height. The gram weight is captured, and chart specifications are provided to the consumer. Each rod is also serialized, making it fully traceable. No stone is left unturned.
Research & Development
Famous NCAA basketball coach John Wooden once stated, “Good things take time, as they should. We shouldn’t expect good things to happen overnight.” This certainly holds true for Wiseco’s Racer Elite connecting rod. The rod was three years in the making, with several major iterations and revisions before being finalized for market. At the start of 2019, Wiseco began working closely on the Racer Elite connecting rod project with Dean Baker, head of engine development at Joe Gibbs Racing Motocross (JGRMX) at the time.
Baker has been in engine development since 1999, spent 11 years at Honda/Yamaha of Troy, three years at Factory Kawasaki, one season at Factory KTM, and recently 12 years heading the engine department at JGRMX. Having been on the leading edge of the modern four-stroke movement, adapting to electronic fuel injection when manufacturers moved on from carburetors, and learning the intricacies of ECUs, he knows his stuff. He also demands the best.
Baker worked with Wiseco to play a role in first developing the needle bearing and cage style Racer Elite rods, since those cover the majority of dirt bikes and ATVs on tracks and trails. Development was then furthered with the plain bearing style rods, targeting today's latest four-stroke engines and racing applications.
“Wiseco did the design work on the Racer Elite rod,” Baker explains. When asked about plain bearing rod development, he commented, “We were able to offer some design guidelines for the operation of the working part of the rod. Things like clearances and interference fit for the bearing shells. We also did quite a bit of research on the surface finish, with regard to what worked and didn’t with the crank pin. You have the connecting rod and the bearing shells that ride on the crank pin. It was figuring out what that surface finish needed to be.”
For example, Suzuki uses a surface preparation on their OEM rod. Baker wanted to find out if that was helpful. Was a regular ground finish, which some other manufacturers use, an advantage? Was DLC coating a benefit? There were a lot of options, and Dean tried them all. In turn, the JGRMX engine developer was able to steer Wiseco in a specific direction while also helping the performance of his own racing spec.
Dean Baker had reference points on the needle bearing connecting rod. He knew the thickness required, cross-section of the rod, and other calculations to confirm what was needed before installation ever took place. Baker also had targets that he wanted to hit as far as performance, which included the weight of the connecting rod. Rod weight is important, as it’s reciprocating mass. You have to accelerate that mass or change directions, which is power-robbing and limits acceleration. From there, Wiseco took over.
Baker was impressed with Wiseco’s engineering group: “Wiseco did a really good job of designing a rod that wasn’t going to have major failures or issues right out of the gate. I didn’t have to really re-work the first or second iteration. It was more of a progression. Some of those minor changes came in the finish work, where we were dealing with a prototype part. Simple things like chamfering edges or relieving oil holes. Those weren’t necessarily big issues, but it gives a nicer part and more durability down the road. The revisions have been passed on to the consumer. Wiseco not only hit the rod weight that I requested, but they also achieved the necessary safety margins.”
Testing at the factory level is an extremely involved and painstakingly thorough process. Every single part installed in a Dean Baker engine must be proved out. The Wiseco Racer Elite rod was put through a minimum of 20 hours of durability testing before Baker even decided to race with it. The rod that made it 20 hours was put through an additional 30 hours of testing, proving its durability for a total of 50 hours, which gave Baker added confidence. They even went as far as to rev a test engine well past its OEM rev limit and the Racer Elite rod came out intact, something that couldn't be said for several other components.
“Race engines have very little time in comparison to test parts in practice engines,” states Baker. “We have our race engines, test engines, and durability engines, whether on the dyno or track. Proving out a part is an evolution, where you sneak up on being confident of a part or question it if failures occur. We have not had any failures with the Racer Elite connecting rod, so my confidence is high.”
As an engine builder, it’s crucial for Baker to have confidence in every part. After all, he’s building a powerplant meant to launch a rider over death-defying jumps and across whooped-out straightaways at breakneck speed. The payoff is hearing positive feedback.
Baker elaborates, “It’s rewarding when the rider comes back and tells me that whatever I had done to the engine is great. In order to utilize a new part, there has to be durability, confidence in the part, and performance gains. If it didn’t have those attributes, then it wouldn’t allow me to take it to the track.”
How exactly did Baker and the JGRMX/Yoshimura/Suzuki team find out they hit a home run with the Wiseco Racer Elite connecting rod? Once again, the rider is the judge and jury.
“In our testing, we build two identical engines with the same port spec, cam spec, and everything else,” explains Baker. “The only difference was that one engine had the Wiseco Racer Elite connecting rod in it. The rider came back and said, ‘Holy cow, that’s the engine I want to race with!’ That’s due to the rod. A rod isn’t a power producer. Instead, think of it as a friction eliminator. There is less reciprocating mass, thanks to the proprietary design. There’s a modest horsepower gain, but it’s more a feel of the connecting rod.”
Dean Baker said it best when providing a general overview of the Wiseco Racer Elite connecting rod, which has since holeshot AMA Nationals and won races.
“The number-one benefit is the quality of the materials used. The OEM rod is a good part, but it’s also built specifically for what the stock horsepower output and RPM range is. If you’re using a Racer Elite rod, it’s taking a step up in allowable performance. It offers higher strength and quality, which are necessary to push the limits of what the engine can do in terms of horsepower and RPM.”
Availability
Wiseco’s Racer Elite connecting rods are available for most newer model Honda, Kawasaki, Yamaha, KTM, Husqvarna and Suzuki motocross-specific four-strokes, as well as the Honda TRX450R and Yamaha YFZ450R ATV applications. Every Racer Elite connecting rod kit includes the rod, OEM-quality crank pin, big-end rod bearing, and thrust washers where applicable. Wiseco also has plain bearing applications available. Find the Racer Elite rod for your model in our growing list of applications below.